Arrangement of dots over the forged piston. — Toyota Corolla II, 1.5 liter, 1990
What to do for those who are not the happy owner of 4g63, ej20 or some beautiful RB with a lot of ready-made tuning solutions - just rustle bills? But to drive quickly and painlessly for the motor so treacherously want ...
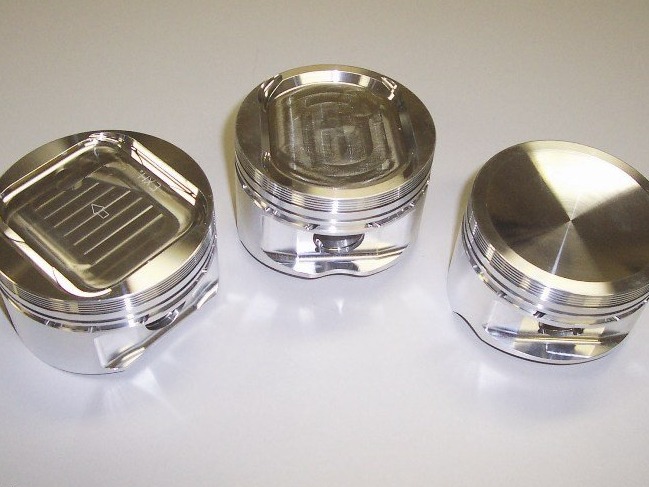
A dear friend of young and all hopeless older people - the Internet - gives 2 answers to this: sit on Tazyaki, for them there is a lot and inexpensively in some MAMI (8-9 thousand for a set of pistons - fuck off!). Or turn around.
Such a difficult choice, but so be it - the second option :)
The sites of some cool and very busy people report that everything is on your 5E / 3E, but on order and 35 thousand rubles. set. We scratch the back of the head, we are looking further. The deductive method reports - outbid.
The callous websites of Russian enterprises dryly report, finally:
Forged pistons (dimensions under the customer's order from 84 mm to 90 mm for foreign cars)
9,500 rubles. Unit meas.: set
Forged pistons to order according to the requirements of the client
Production time is about a week from the date of receipt of the advance payment.
Piston diameter from 84 mm to 90 mm.
Piston configuration is discussed additionally according to the customer's specifications.
The price is for a set of pistons 4 pcs.
The piston is made from a piece of aluminium.
steel material - AK12.
Additionally, the Molykote anti-friction coating is applied to the surface, which provides longer-term protection of the pistons from wear and reduces friction during the preliminary running-in of the car.
this link is not an advertisement www.meta-s.ru/product_902.html
Moreover, some have blanks from 60 to 93 mm, and the material is possible AK4.
boring things about AK12 and AK4 >>>>>>>>>>>>>>>>>>>>
A typical silumin is the AL2 (AK12) alloy with a content of 10-13% Si. In the as-cast state, it consists mainly of eutectic and some excess silicon crystals. The mechanical properties of such an alloy are very low: sv = 120 - 160 MPa with a relative elongation d < 1% (table 2).
However, these alloys have very important properties that are difficult to achieve in other stronger alloys: high fluidity, weldability. They have low casting shrinkage, and therefore their tendency to shrinkage cracks becomes low. Silumins, due to the small difference in the solubility of silicon at high and low temperatures, are practically not hardened by heat treatment, so the most important method for improving its mechanical properties is modification. Modification is carried out by treating liquid silumin with small amounts of metallic sodium or sodium salts. During modification, a significant refinement of the particles of the eutectic mixture occurs, which is associated with the ability of sodium to envelop the formed silicon nuclei and inhibit their growth.
In addition, some supercooling was noted during the modification, which corresponds to the occurrence of eutectic transformation, and the eutectic concentration shifts to the right. Thus, hypereutectic alloys lying somewhat to the right of the eutectic point turn out to be hypoeutectic after modification. The structure of the alloy after modification turns out to consist of excess crystals of an a-solid solution and a very dispersed, almost point-like eutectic.
Possessing high casting properties, silumins are the main source material for the creation of technological and, at the same time, high-strength cast aluminum alloys, which can be subjected to hardening heat treatment. When creating such alloys, additional alloying of silumins is used in order to form new phases in the silumin structure that can lead to hardening during heat treatment. Mg, Cu and Mn are used as such elements. On the basis of such alloying, cast aluminum alloys are currently created and used: AL4 (9% Si, 0.25% Mg and about 0.4% Mn) and AL5 (5% Si, 1.2 Cu and 0.5% Mg ).
The strength of these alloys after quenching and aging is higher than 200-230 MPa with elongation d ³ 2-3%. The effect of hardening of alloys during quenching and aging is explained by the formation during aging of Guinier-Preston zones and intermediate phases of complex composition, which differ in composition and crystal lattice from equilibrium, for example, Mg2Si, and coherent with the solid solution by their crystal lattices.
Alloys of the Al-Cu-Mg system with additions of iron and nickel (AK2, AK4, AK4-1) by appointment belong to the group of heat-resistant materials. In terms of their chemical and phase composition, they are very close to alloys of the duralumin type. The main strengthening phases during the heat treatment of these alloys, as well as for duralumins, are the S and θ phases. The difference lies in the fact that instead of manganese, iron, nickel and silicon are contained in significant quantities as alloying elements. Alloys are less alloyed with copper.
With the addition of iron to the alloy 2% Al; 1.6% Mg, the strength properties are sharply reduced, iron forms an insoluble intermetallic compound Cu2FeAl7 with copper, which reduces the concentration of copper in the solid solution, thereby reducing the strengthening effect. Additions of nickel, which forms a practically insoluble ternary phase with copper Al6Cu3Ni, have a similar effect. However, with the simultaneous introduction of iron (up to 2.5%) and nickel (1.6%), a sharp increase in the strength properties in the hardened and aged state is observed, while the maximum values ​​are achieved at an iron content of 1.6%. At other concentrations of iron and nickel, the maximum values ​​of strength properties are found at a ratio of iron and nickel equal to approximately 1:1. Iron and nickel form the ternary compound FeNiAl9, which reduces the possibility of formation of insoluble compounds AlCuFe and AlCuNi, which increases the concentration of copper in the solid solution. With an increase in the content of the FeNiAl9 phase in the alloy, the effect of heat treatment increases. The FeNiAl9 phase improves the conventional mechanical properties and heat resistance of the alloy.
>>>>>>>>>>>>>>>>>>>>>>>>>>>>>>>>>>>>>>>>>>
As I understand it, this is the difference between "soft" and "hard" forging?
The last trick with the ears is about the dimensions that the manufacturer needs to know. Beauty didn’t work out - I didn’t find a drawing template, but it is on the net, because TEXT :)
geometry for children>>>>>>>>>>>>>>>>>>>>>>
In order to make a piston, you need to know several of its geometric dimensions:
1. The diameter of the piston
2. The number and size of tsikkov (holes) under the valve (16-valve engine - 4 pcs, 8-valve engine - 2 pcs.)
3. The volume of the combustion chamber in the piston.
4. Piston pin diameter.
5. Size and number of piston rings (ring thickness)
6. Width of the upper connecting rod boss.
7. Compression height
Compression height (Cx) = block height - connecting rod height - crankshaft stroke / 2
>>>>>>>>>>>>>>>>>>>>>>>>>>>>>>>>>>> >>>>>>>
Which hero will tell you how to defeat the feature- "folding" part of a long record? It turns off, but the problem is with the opposite ...
and we have a diameter of 73mm. So they will not make such pistons. Bummer :( Are there any other options? I re-read, not only 84-90 but also 60-93. I wish you success!
on 3e motors, the piston diameter is 73.8 to be exact, and 4e is 74, so it is quite possible to use it as a repair.
15 thousand rubles ... the price of the issue. They are in Vladivostok, in a tbning shop (I don’t know the name). is on 2E, 3E. and no need to be smart at the factories