SilektrS SR_PB81 (cross beam reinforcement kit) - Toyota Mark II, 3.0 liter, 1990
Since we are installing a heavier motor in the car and are going to drift, the loads on the cross beam increase significantly, and this affects the transmission of torque from the engine and the controllability of the car in general. Due to the increase in engine weight, the vertical load on the beam increases, and due to the increase in engine power, the torque relative to the longitudinal axis of the vehicle also increases and, accordingly, the beam becomes more pliable for twisting. Also, going sideways increases the lateral loads from the lower front arms, which, as we know, are bolted directly to the beam. Initially, when we took the beam in hand, the idea was to increase the reliability of the lugs to which the lower levers are screwed, since their metal is very thin in my opinion. Well, then, having calculated all the options and having estimated on the spot, we decided to make a complete kit for reinforcing the SilektrS SR_PB81 beam. The weight of the whale turned out to be 2.4 kg, taking into account welding, but it significantly increases the reliability of the part on which it is installed, and also increases the rigidity of the beam as a whole. It was the lower chord of the beam that was strengthened, since it is known from the theory of the calculation of bridges that it is he who suffers with an increase in load, and there are also expansions in the center to reduce the pliability of the beam to twisting.
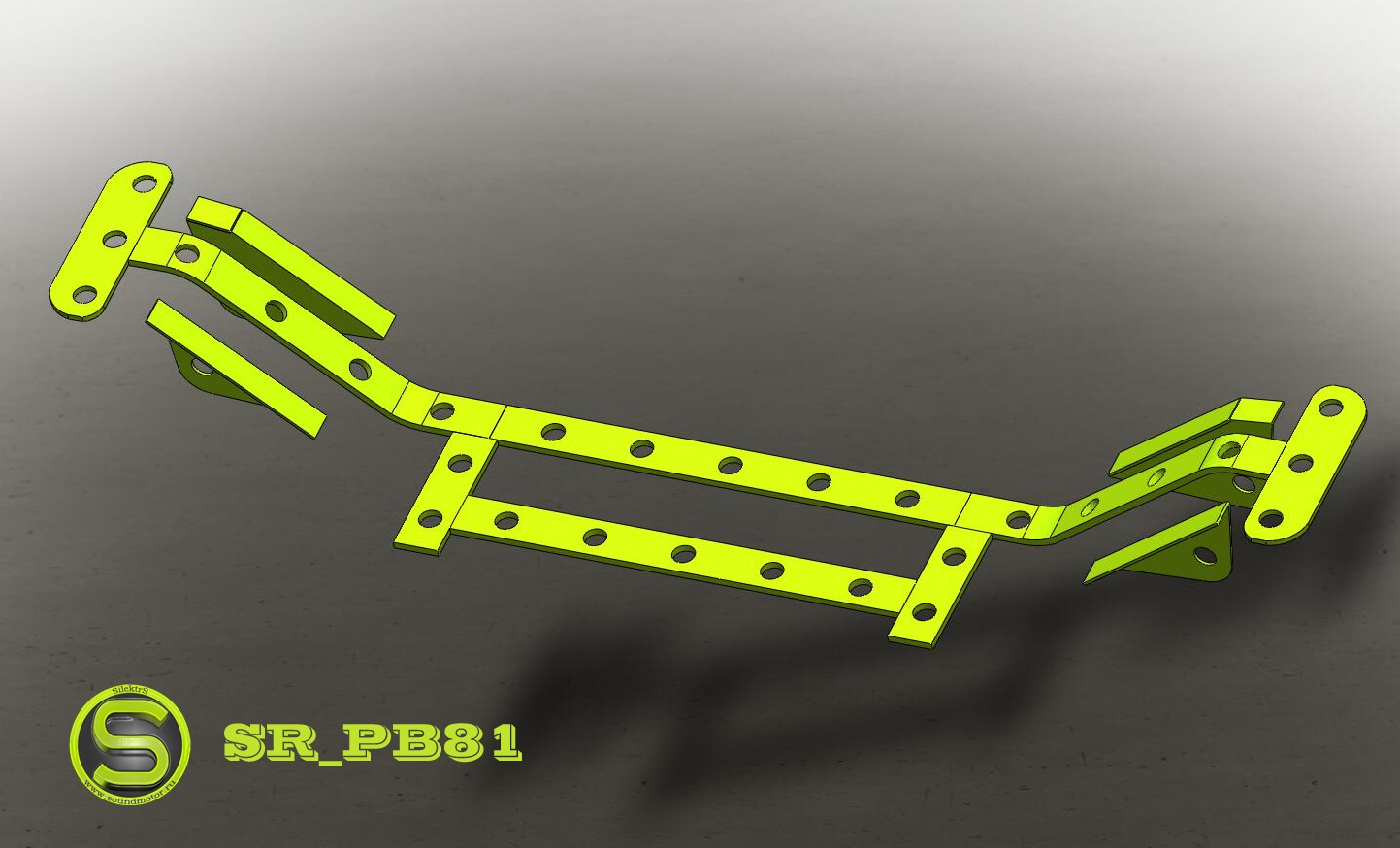
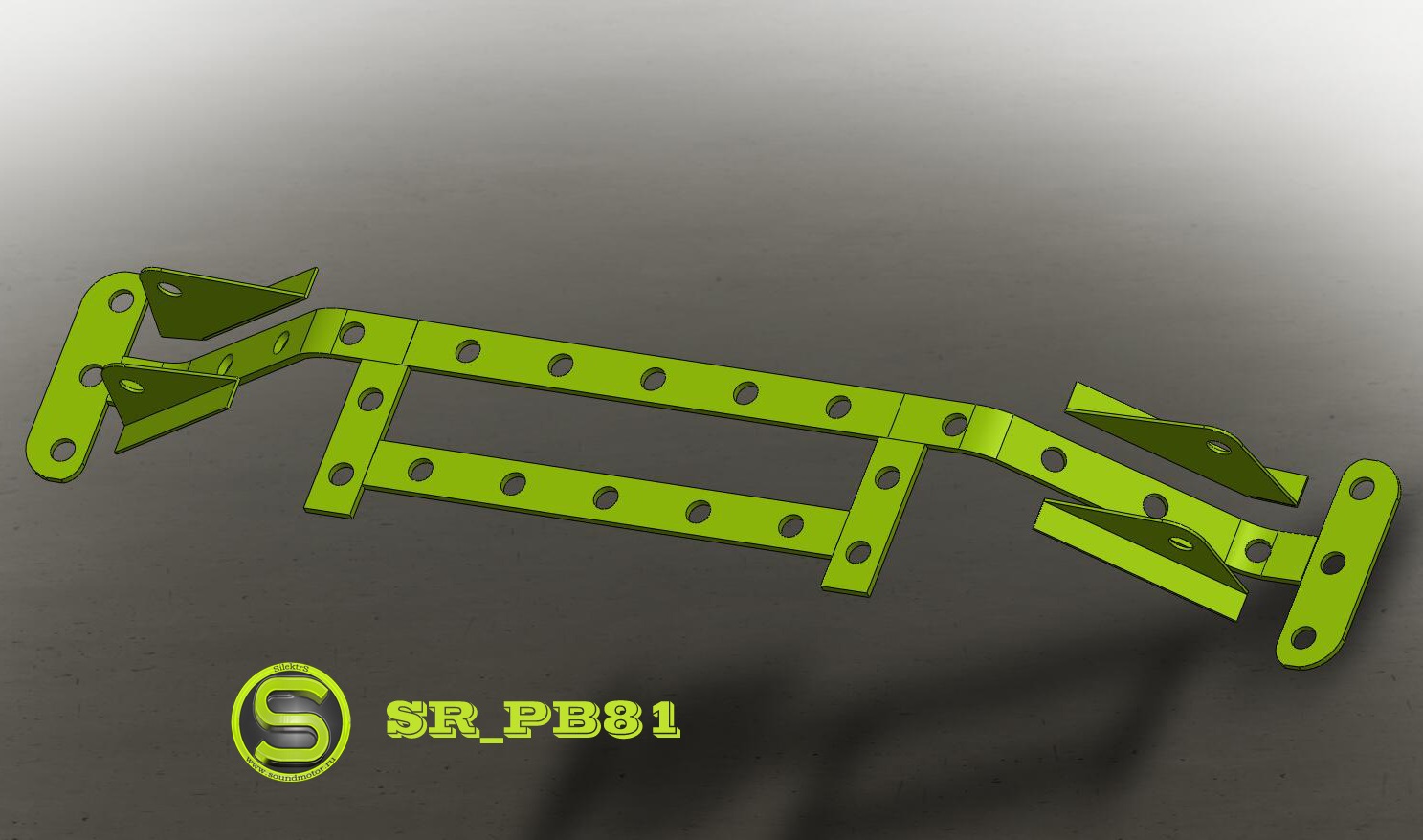
Initially, we have a stock beam, which we carefully clean and clean from old paint for the convenience of welding.
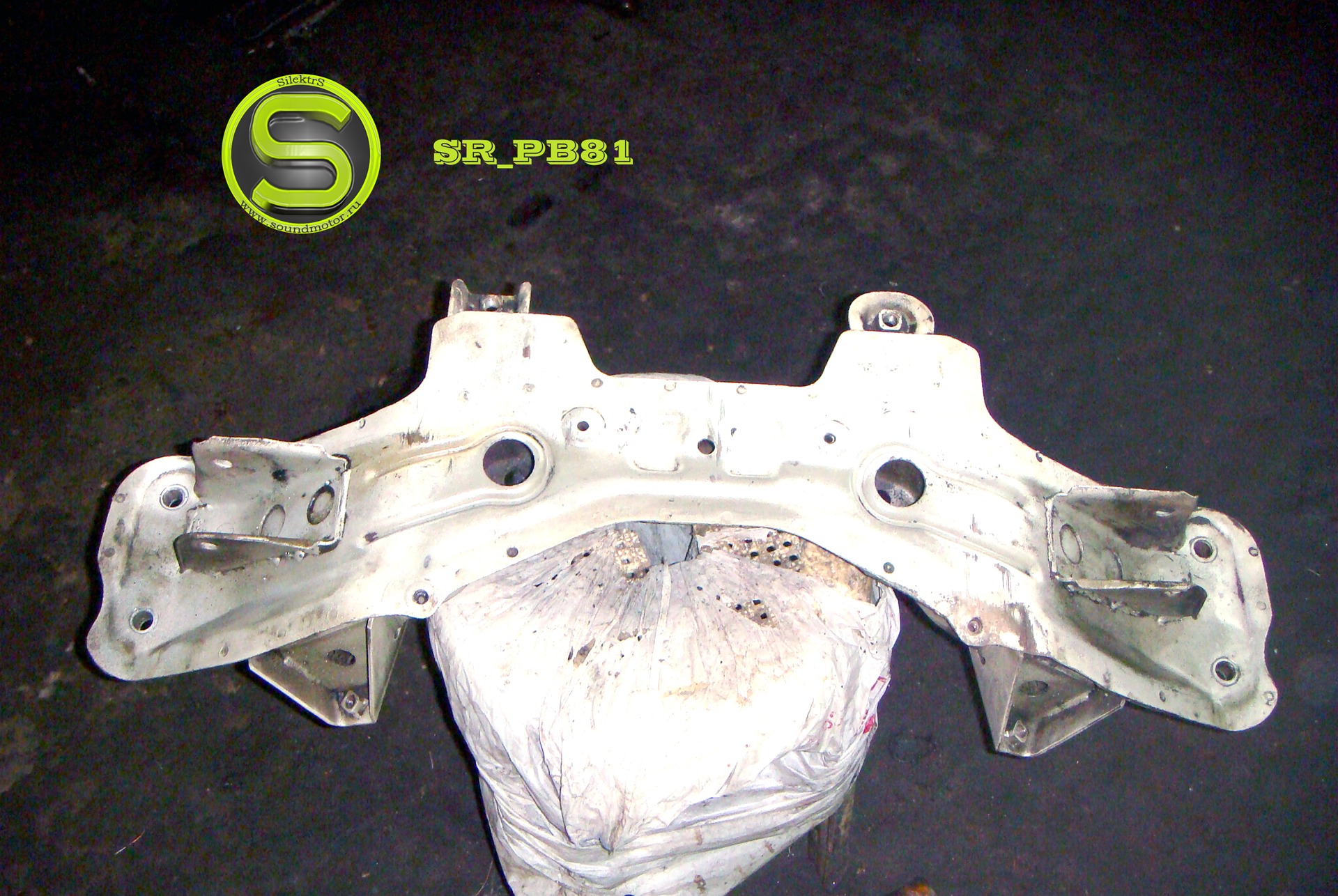
Then, after prototyping and fitting, we make a reinforcement kit. The thickness of the lower plastites is 5 mm.
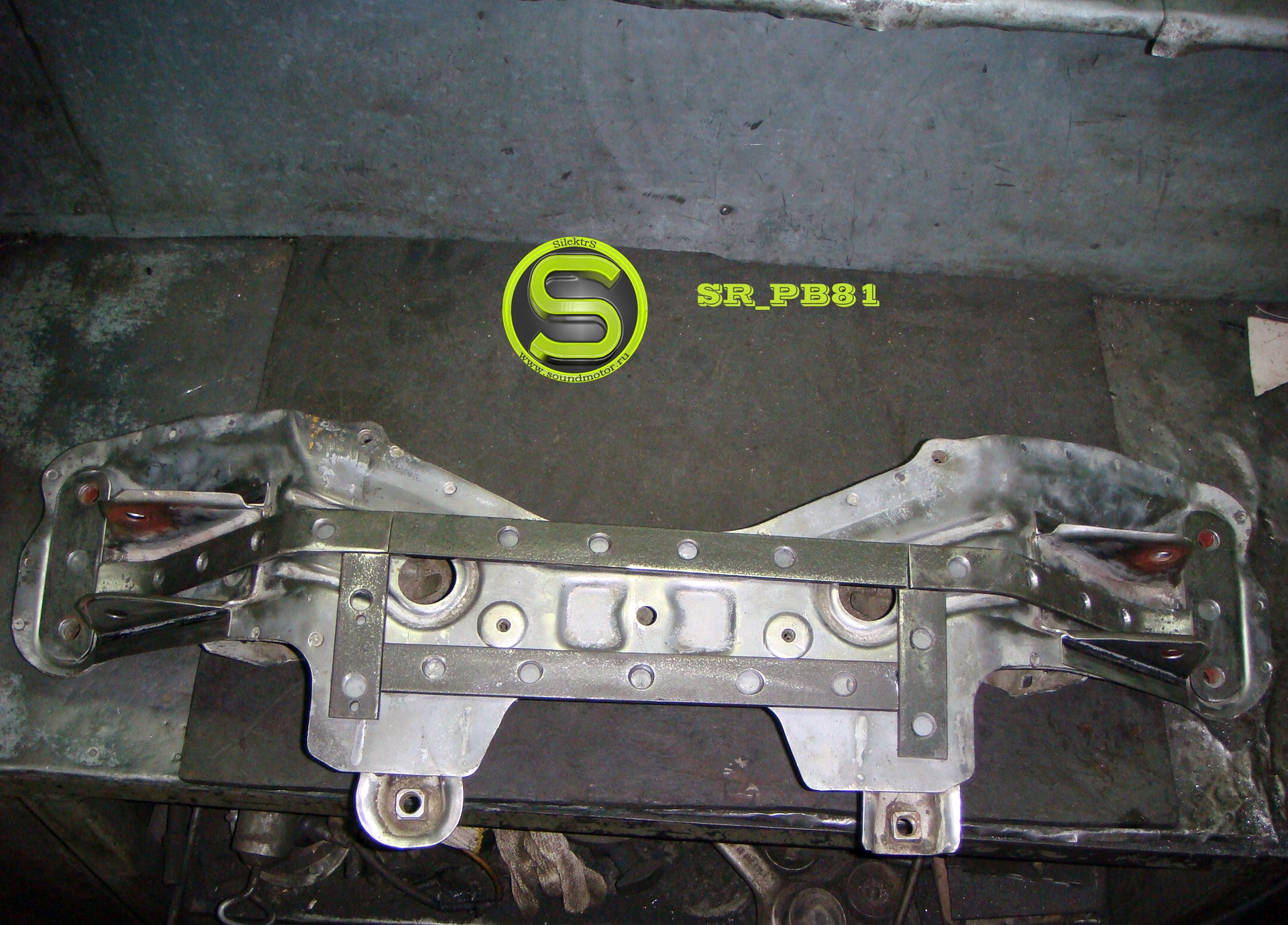
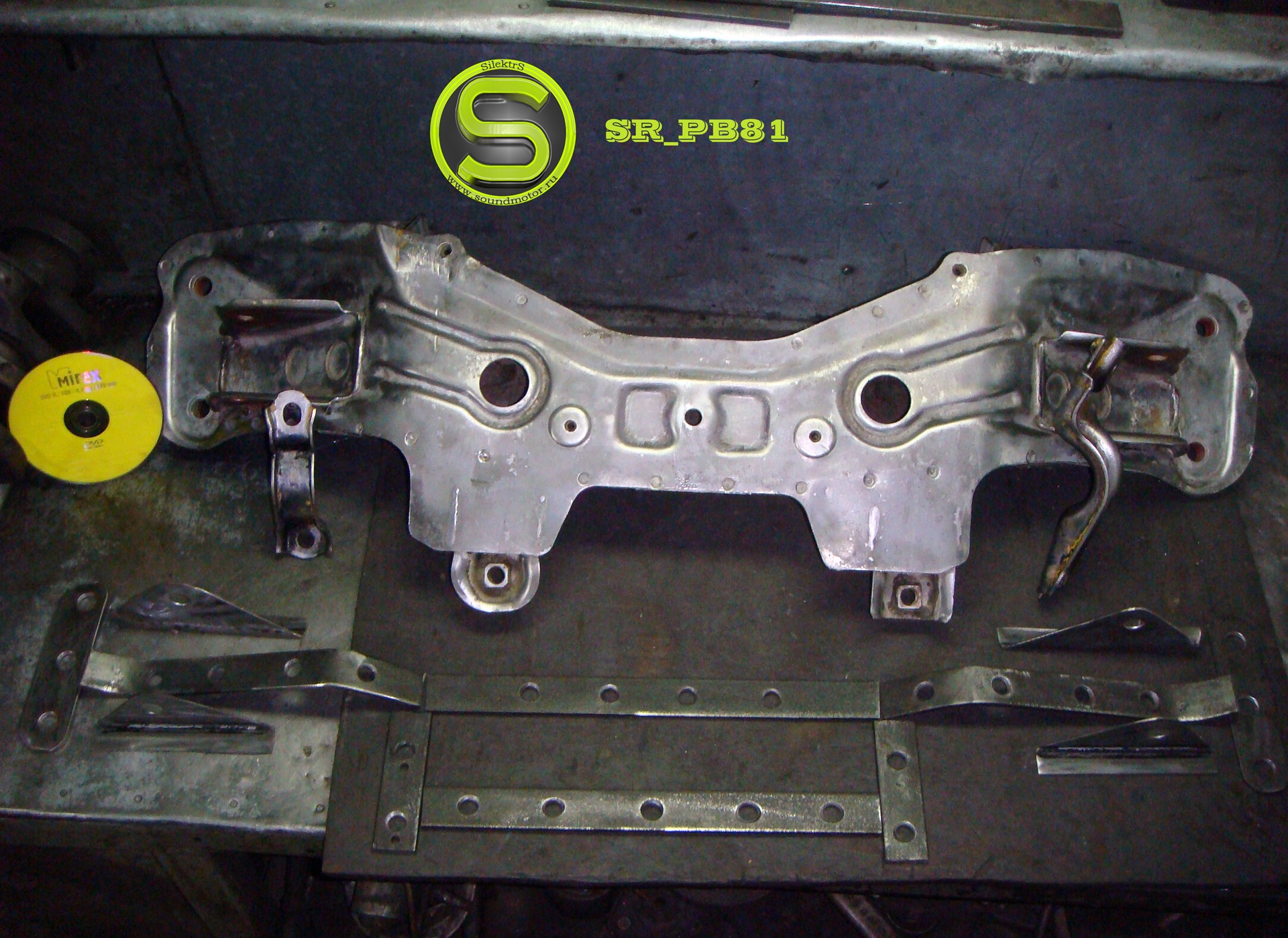
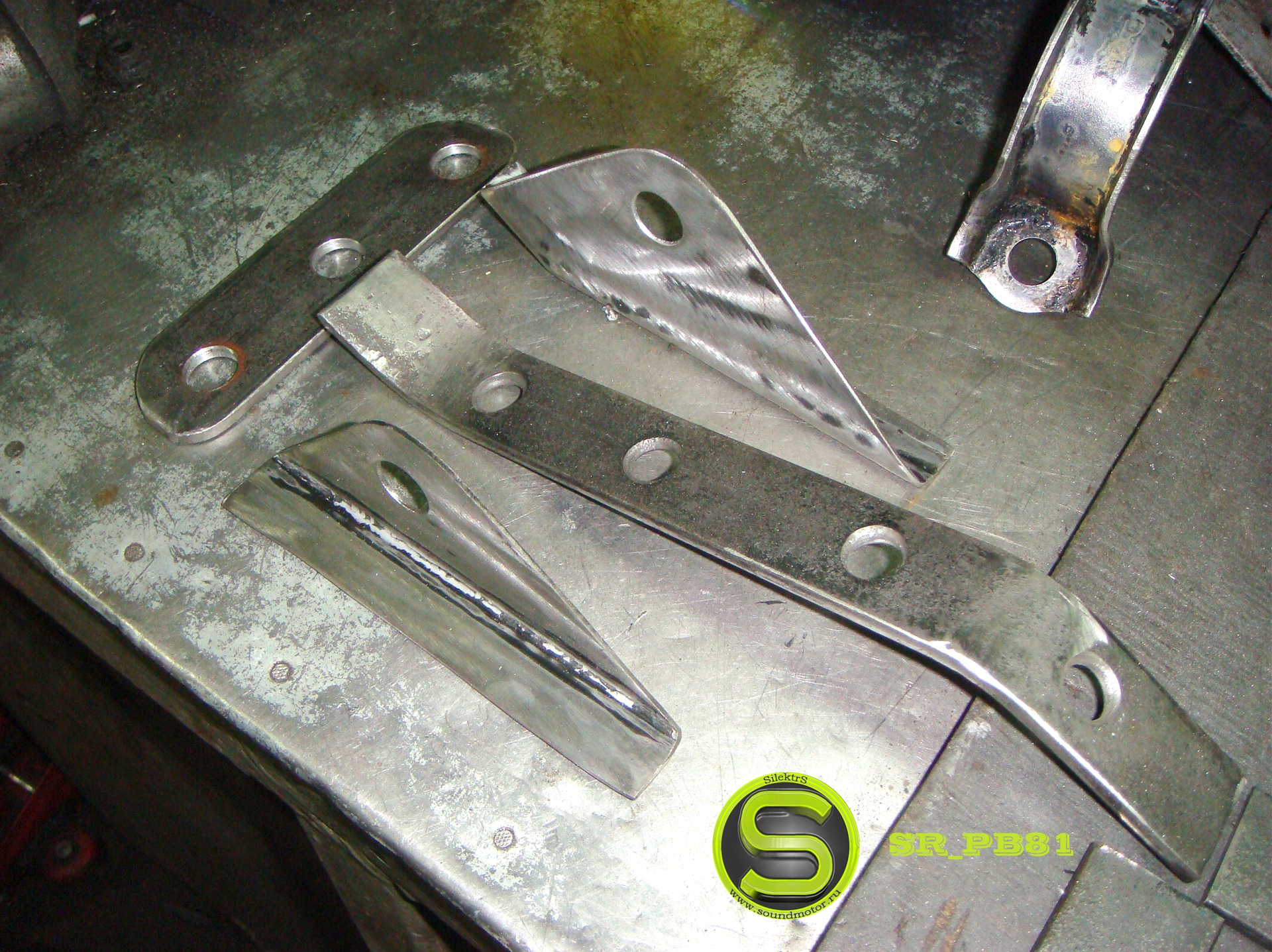
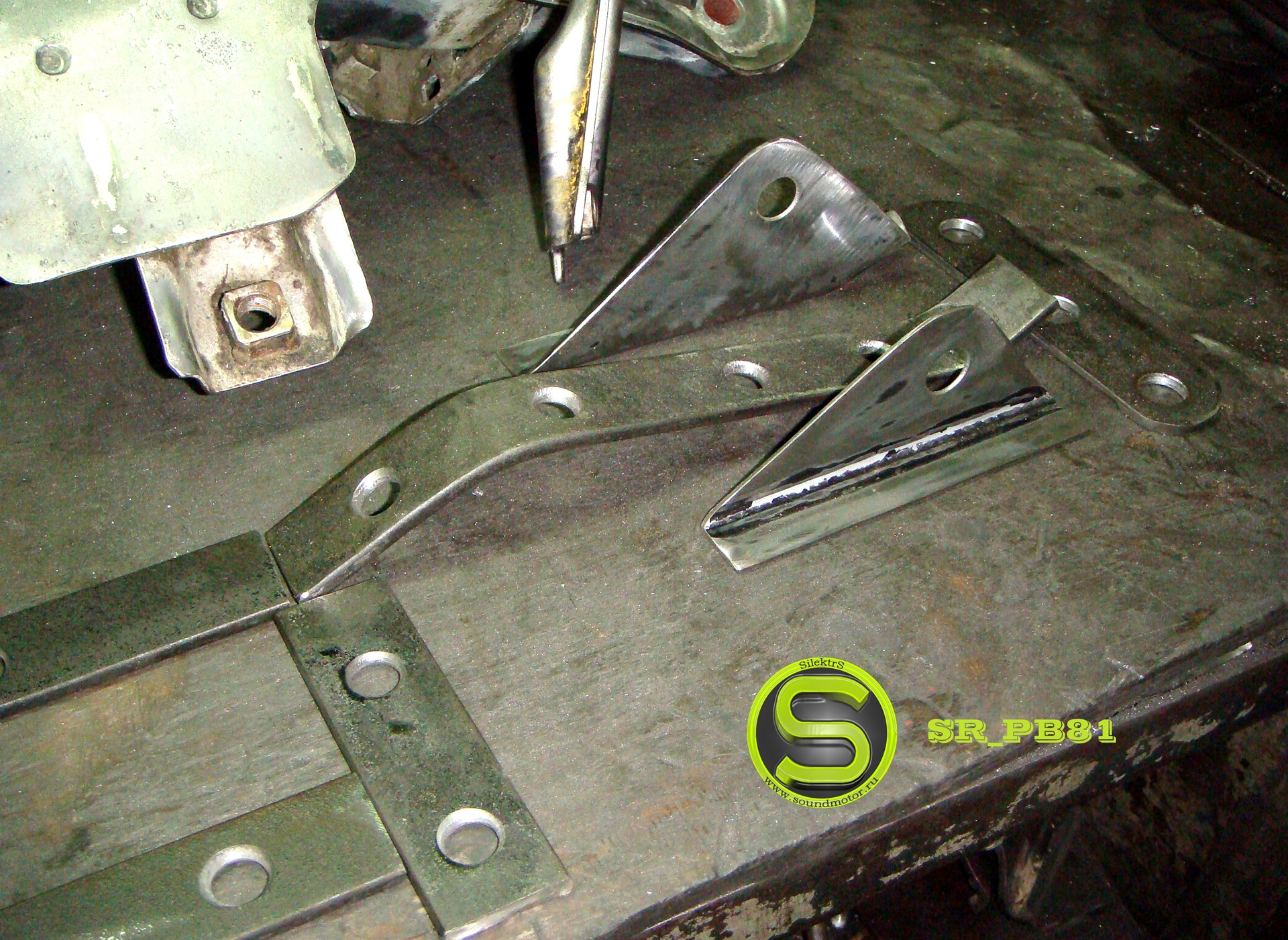
After fitting, we weld the elements of the whale to the beam.
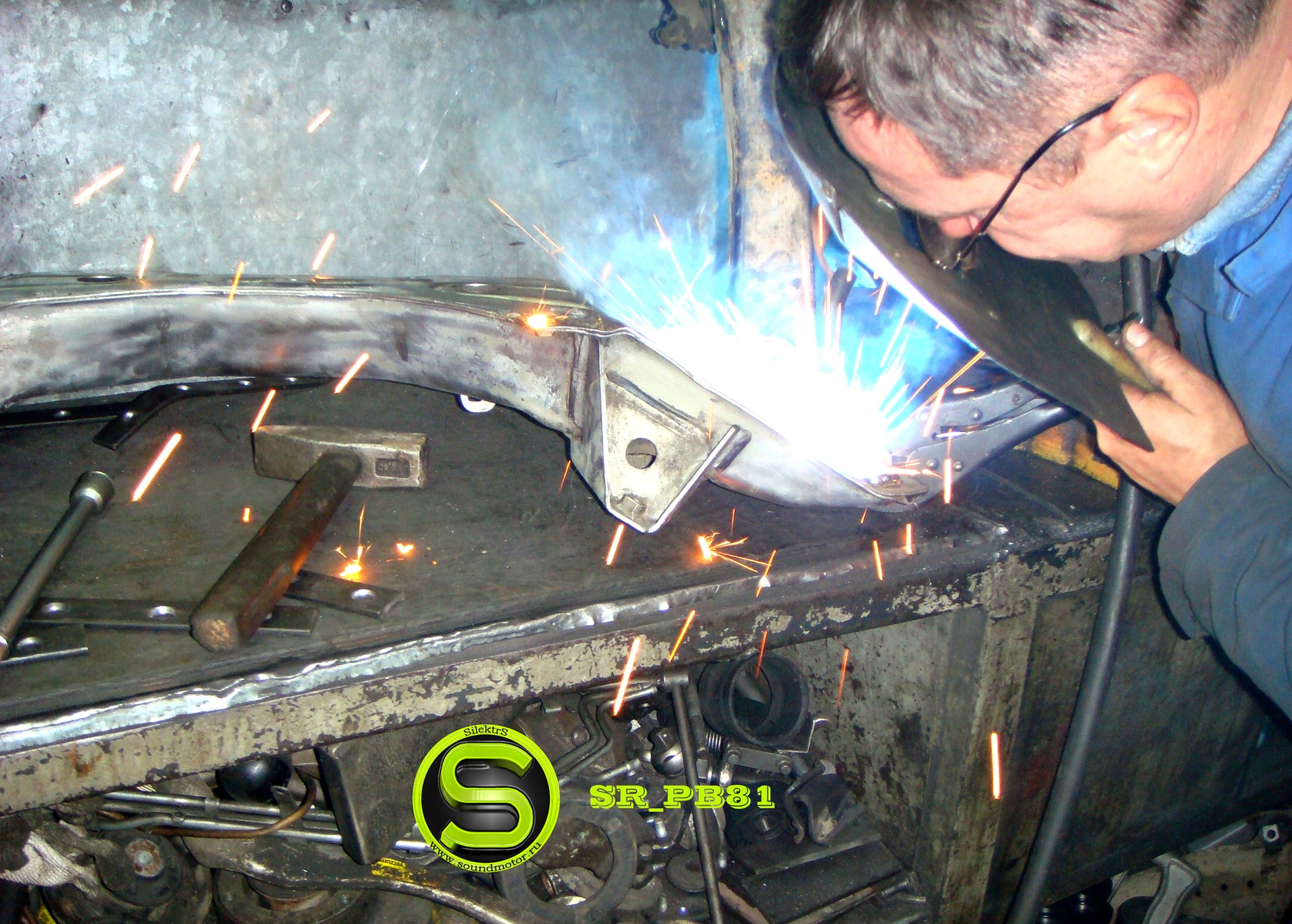
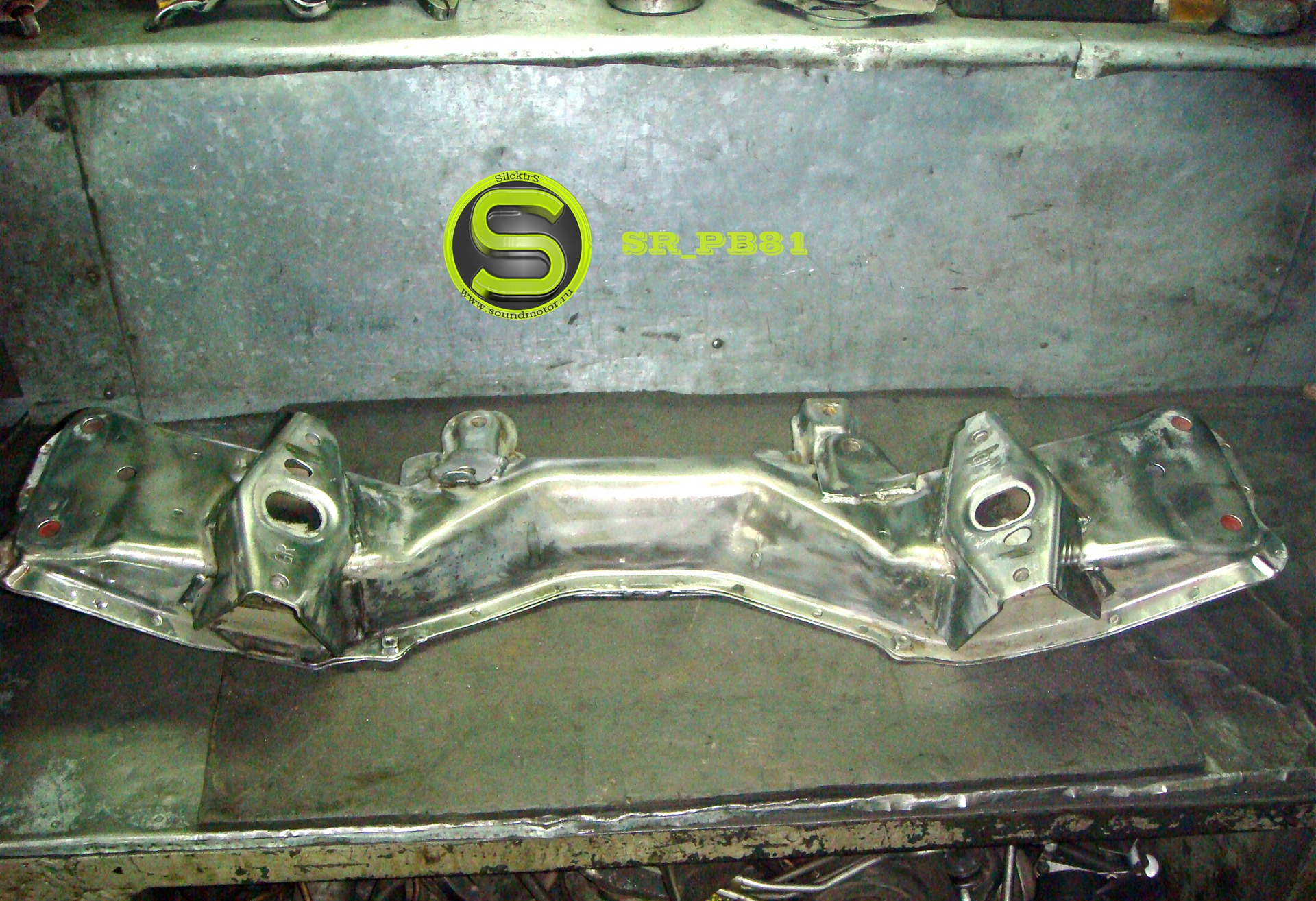
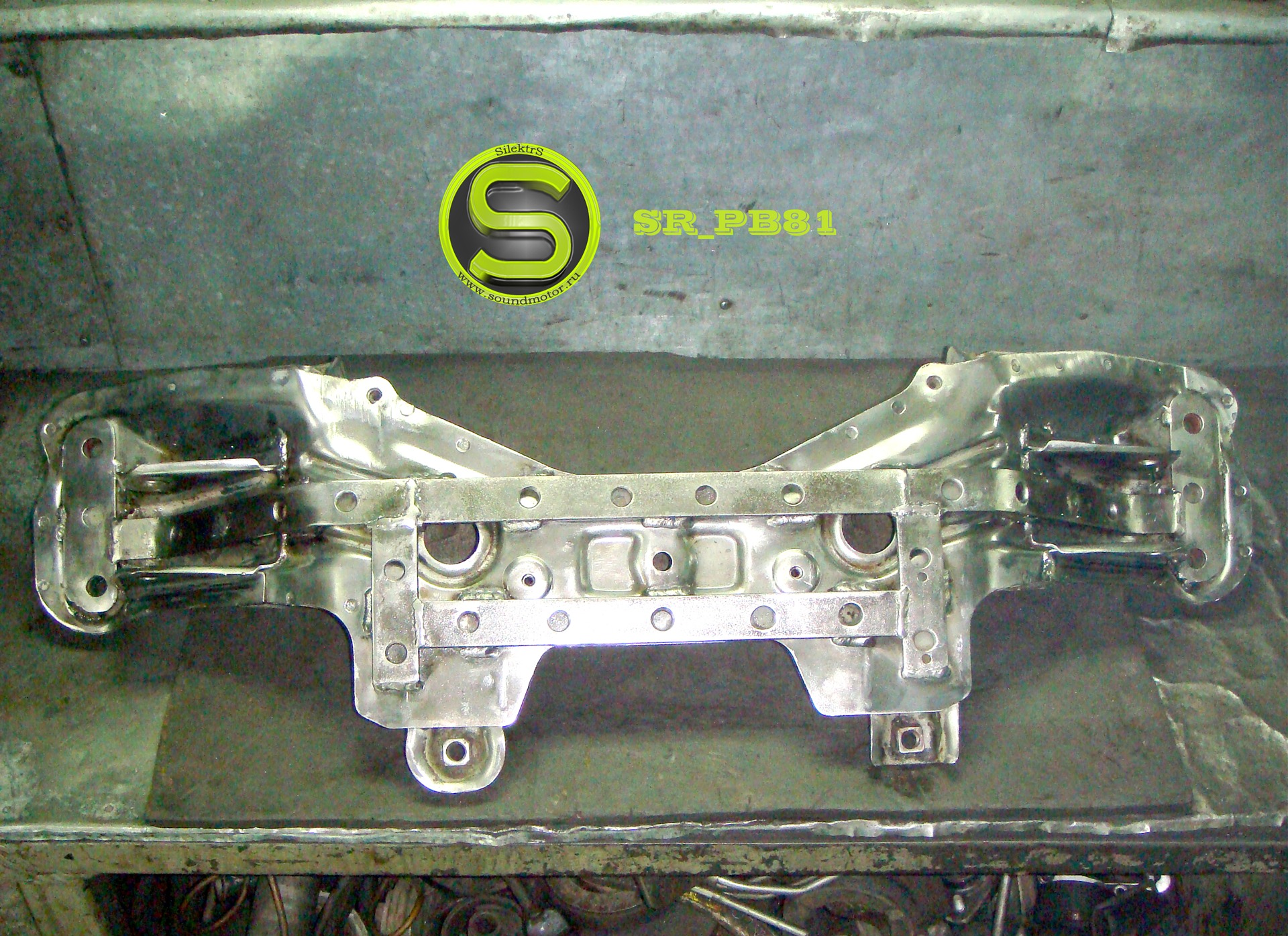
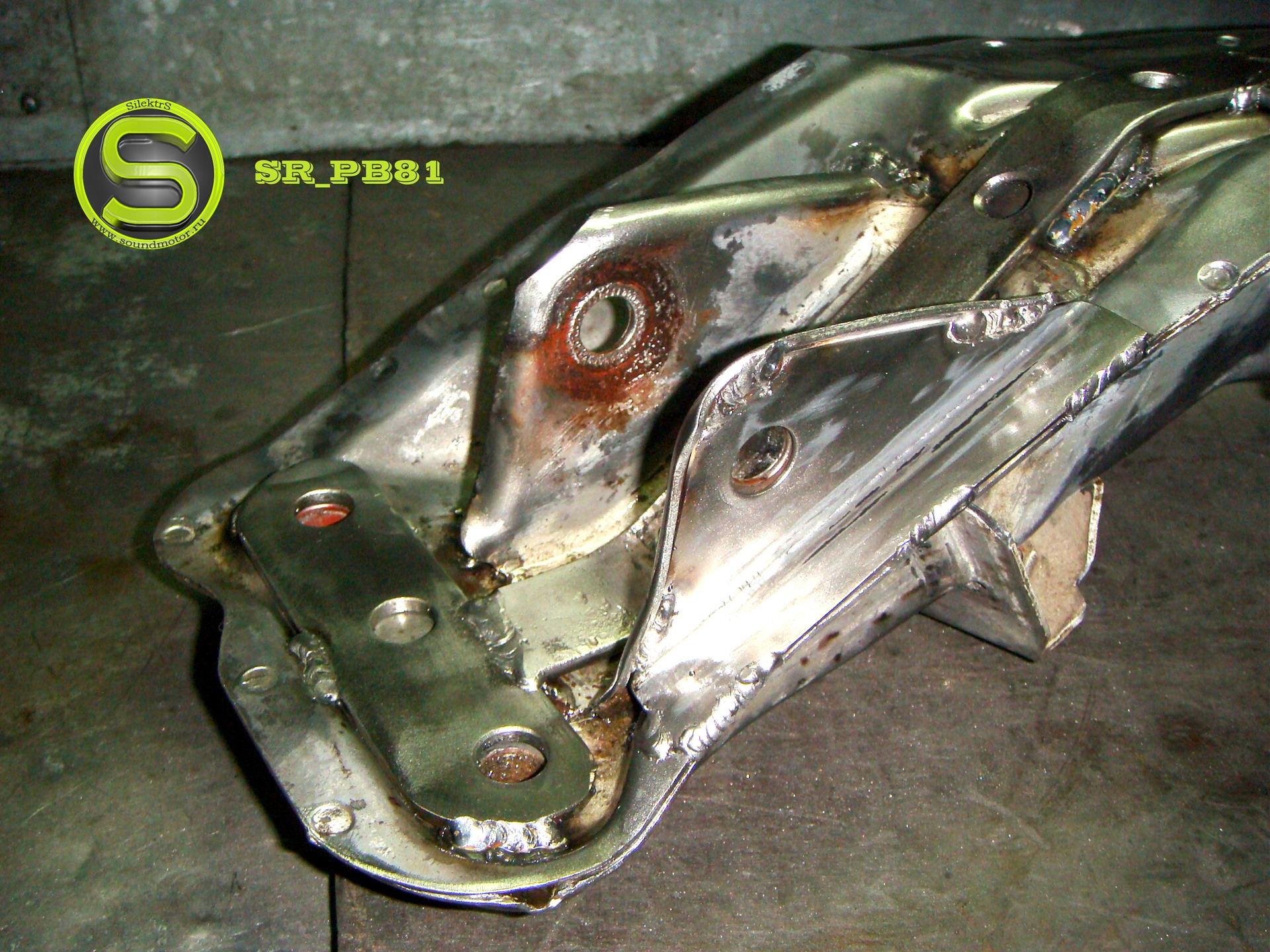
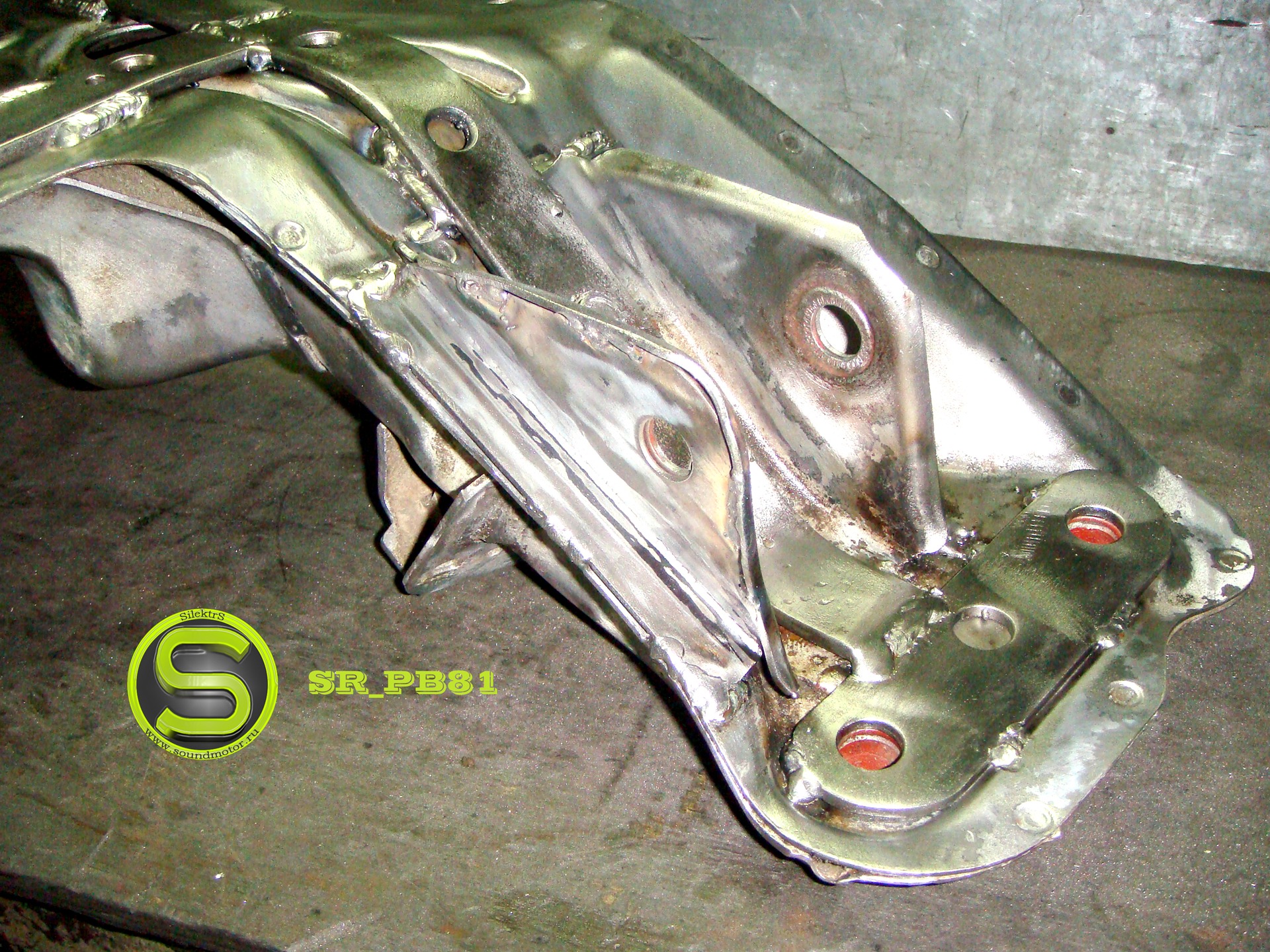
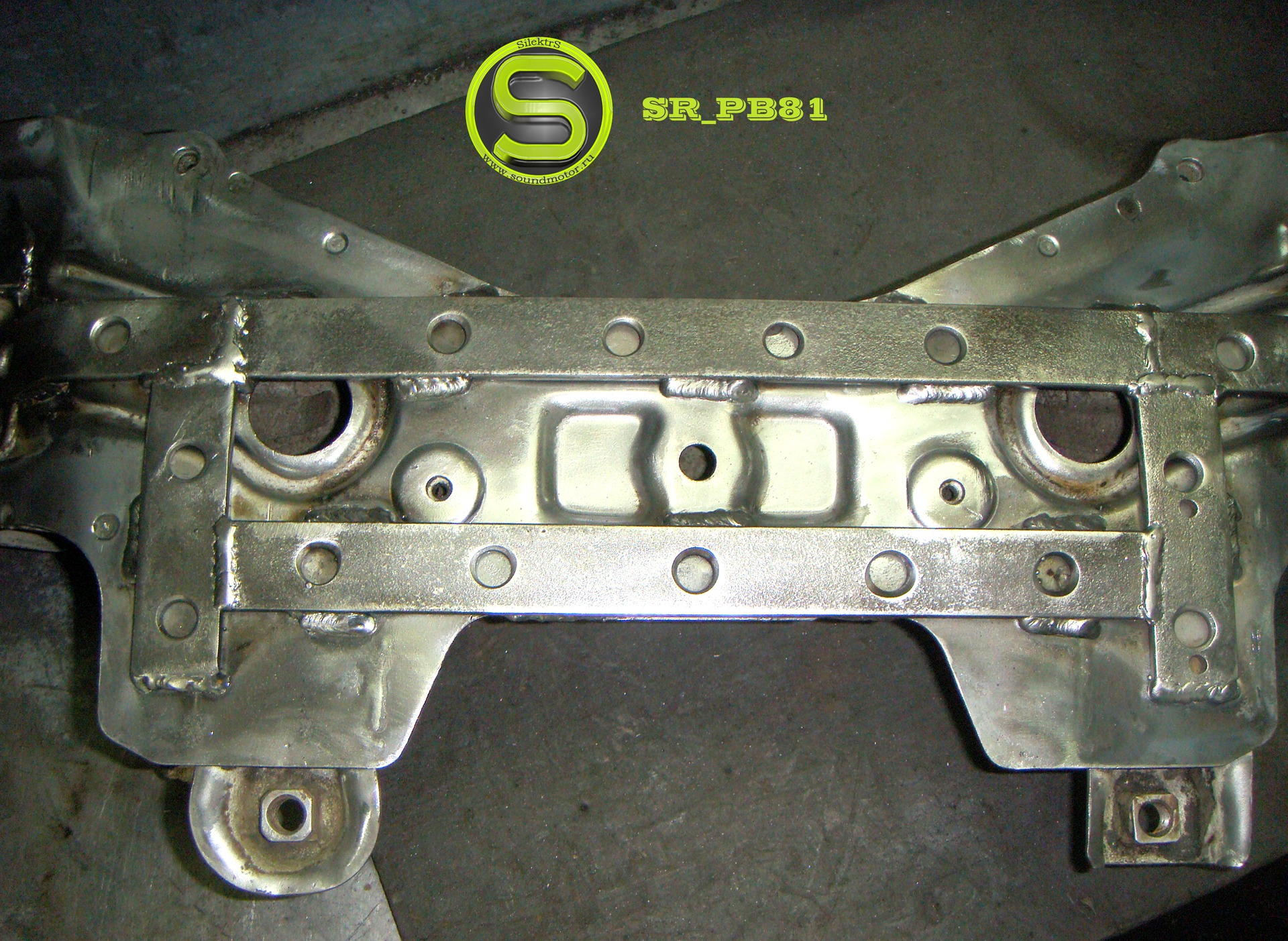
After welding, we prepare the surface and apply several layers of primer with preliminary drying.
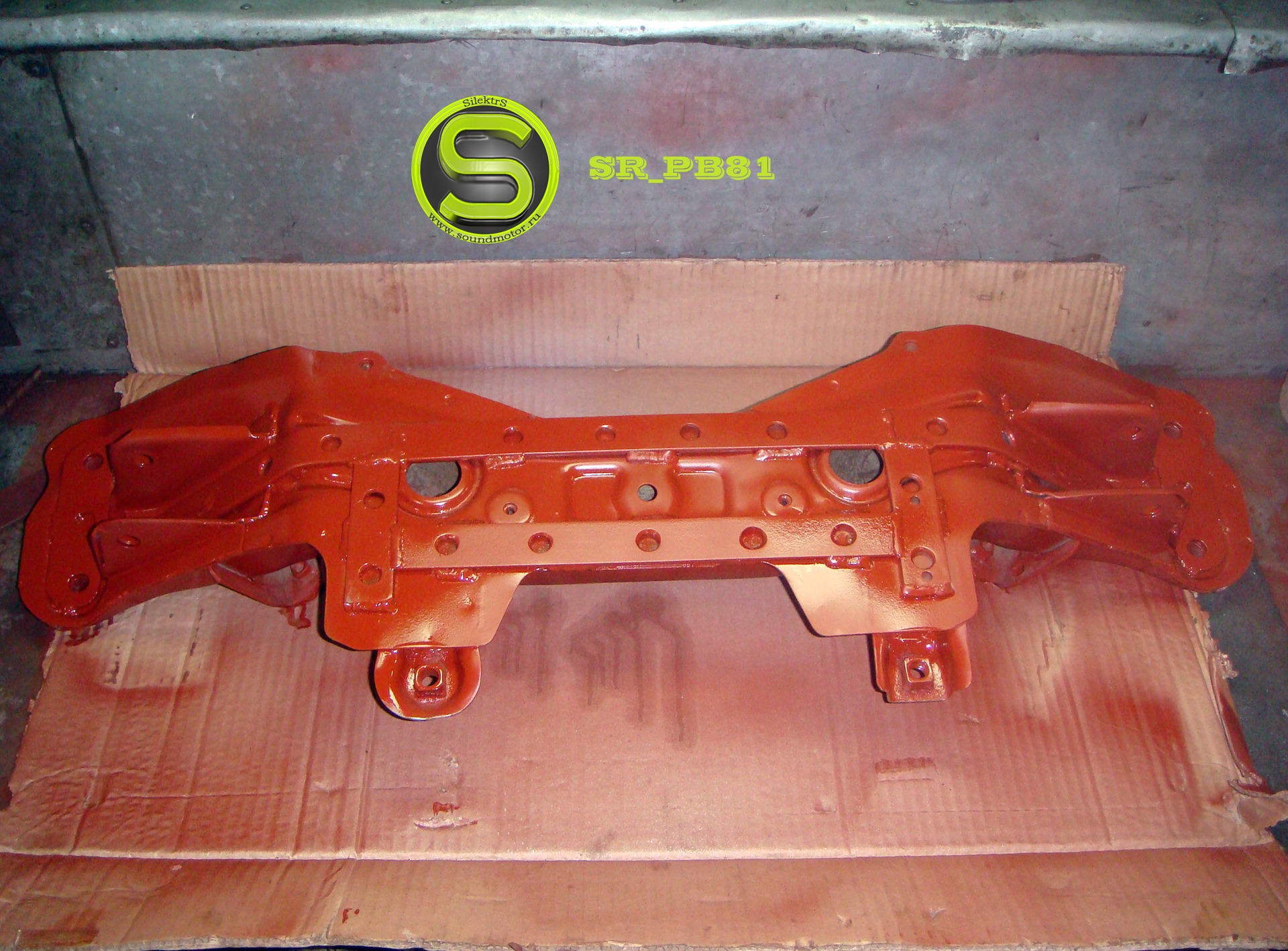
And finally, a beautiful detail!
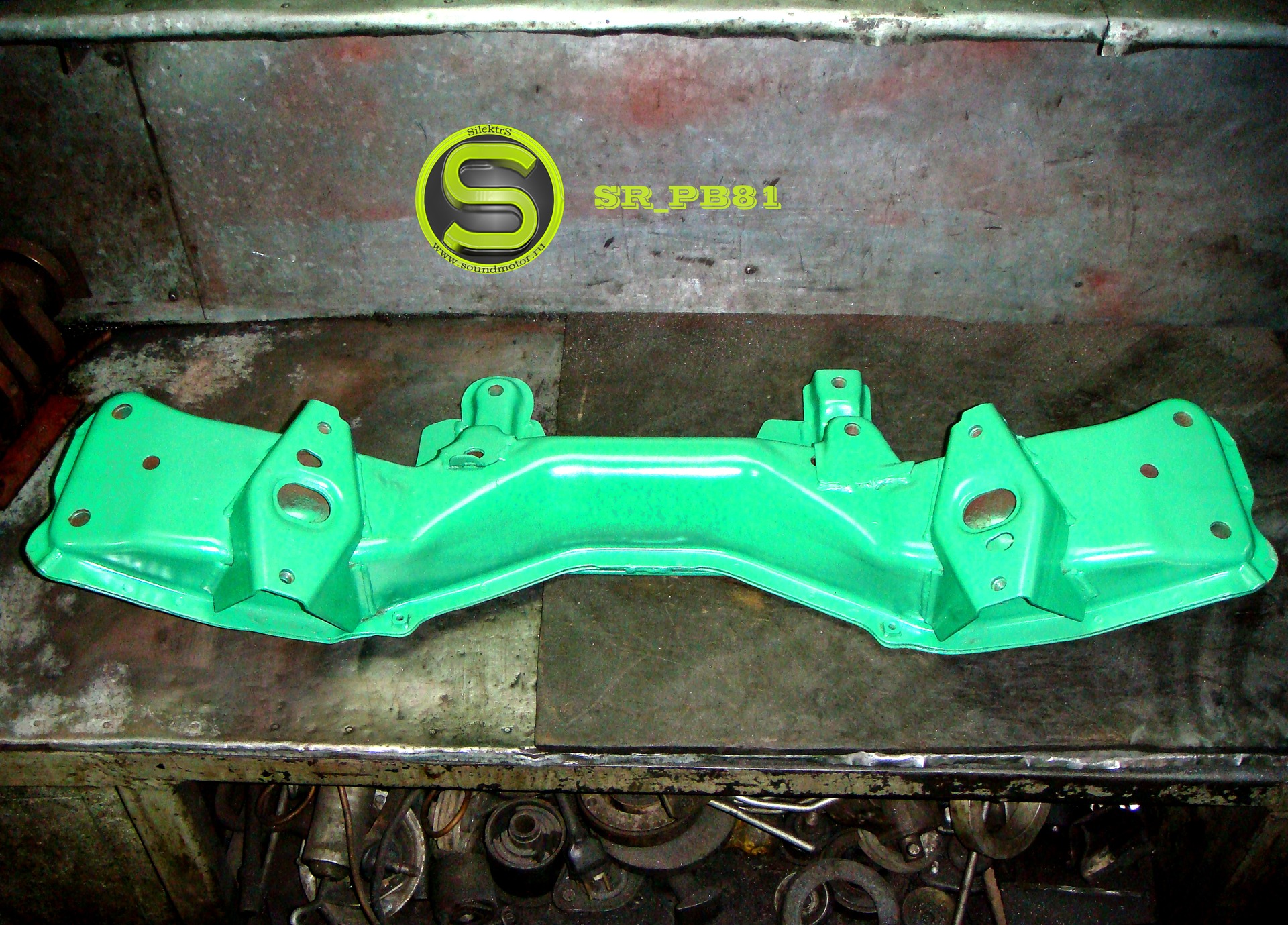
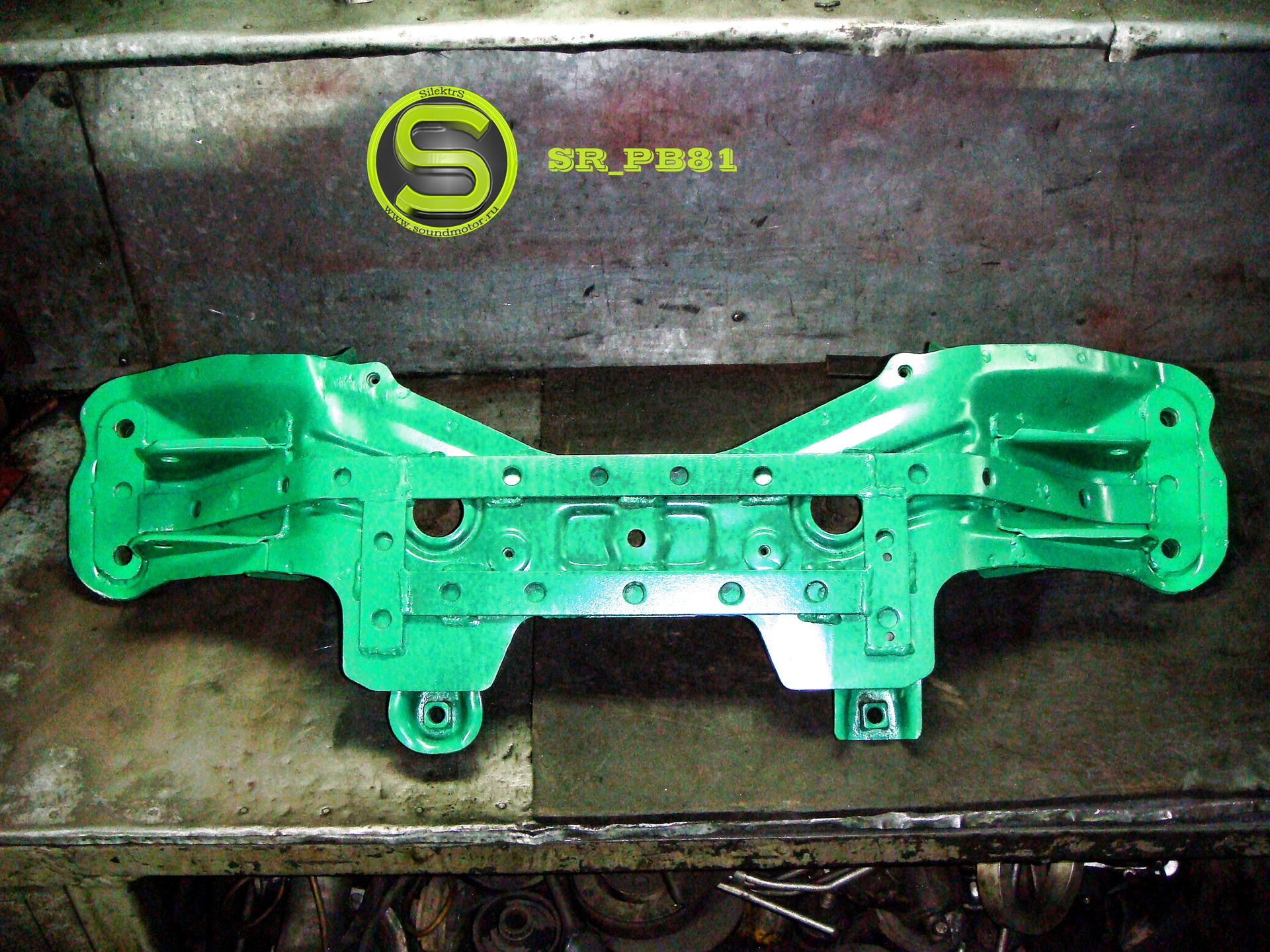
In conclusion, I want to express my deep gratitude to my father-in-law Nikolai Aleksandrovich, who developed the concept and also made the amplification kit itself.
Al-exe
as I understand it, the calculations were made, well, by what percentage did the stiffness increase? at least 5% is?
The calculations were estimates, but I think more than 5%, probably 10 percent)
vitekV
I think more. there is a paper beam, and here the metal is much thicker
all on point)
engineers of course well done, but I think they hardly imagined the conditions under which the machine will be used) Silent blocks I think will be AL.
Well, I’m also not just saying from scratch, we studied it ... I agree about the lever bracket, the benefits will be noticeable ... again, will you also put hard silent blocks there?
it’s just that the engineers were not stupid to make this beam, they all calculated, I don’t think that the beam from 7m or 1zhz differs fundamentally from 1zh, except for the engine supports themselves ... although these are Japanese, they could do another ... but I think it will be problematic to model the beam itself :)
but if you suddenly find time and you will carry out the calculations, then it will be a hellish megarespect!
but I think it will not be superfluous and such an increase
Al-exe
there are vertical ribs, in this case, nifiga, I don’t see the point in such an event, it’s better in this case to put some thread on the bottom spacer ... well, in general, the calculation should show whether it makes sense ... again, do not forget about the metal stresses in places welding, was there any post-processing ...
When we design metal bridges, and this is exactly what I do, the main emphasis is on the lower chord of the main beam, since it is responsible for the rigidity of the entire structure under the action of a vertical load. It is usually made much thicker than even the web of the beam. The same trend can be traced here, since the loads from the motor increase significantly, because it weighs much more than the stock one. And then imagine how these loads increase when you drive over bumps, you can say you jump especially when you have rigid racks and even more rigid engine mounts! I believe that with such reinforcement, the lower strut is not needed! I did not do a full calculation, because for this it is necessary to model the entire beam and calculate it first without amplification, and then with amplification and compare the results, but this is very painstaking work and takes a lot of time,
that's why we welded with a dotted seam, and the stresses are not so big. In normal drift cars, all factory seams are boiled.
vitekV
metal is always tense with our roads :)) by the way, do you still have a beam with crosses?
I gave it to Misha.
about the stresses of metals as a result of heat treatments, I still think it’s worth remembering a little :)
metal is always tense with our roads :)) by the way, do you still have a beam with crosses?
there are vertical ribs, in this case, nifiga, I don’t see the point in such an event, it’s better in this case to put some thread on the bottom spacer ... well, in general, the calculation should show whether it makes sense ... again, do not forget about the metal stresses in places welding, was there any post-processing ...
as I understand it, the calculations were made, well, by what percentage did the stiffness increase? at least 5% is?
usually on serious machines, the beam is generally changed to a full-fledged subframe, because stamping is stamping!
What prompted you to look for such a solution? were there really precedents when the beam was bent?